Scaling RAG Systems in Financial Organizations Artificial intelligence has emerged...
Read MoreAI-Powered Process Optimization: Boosting Efficiency in Manufacturing
Table of Contents
ToggleIn the manufacturing sector, process optimization is crucial for driving productivity and fostering sustainable growth. To achieve these objectives, stakeholders increasingly rely on a variety of technologies and software solutions.
Among these, artificial intelligence has emerged as a transformative force, offering unparalleled capabilities in optimizing manufacturing processes. By using AI to analyze large datasets, manufacturers can improve decision-making and streamline operations. This helps them find new efficiencies. AI is now a key part of modern production strategies.
A McKinsey report shows that companies using AI have seen a 10-15% boost in production. They also report a 4-5% rise in EBITA, which stands for Earnings Before Interest, Taxes, and Amortization.
Find out how papAI can improve the deployment of AI projects in the Manufacturing Industry.
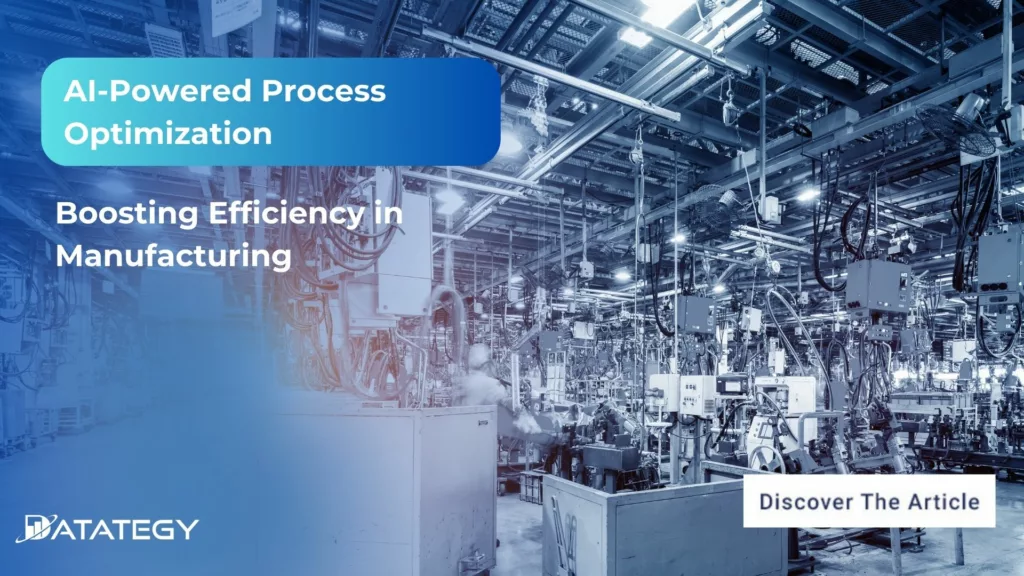
In this article, we will explore how artificial intelligence (AI) enhances process optimization.
What does AI Algorithms in Manufacturing Mean?
The digital revolution in the industrial sector is mainly driven by AI algorithms. These smart computer models help robots analyze data, find patterns, and make predictions. In the past, only human experts used these tools.
Artificial intelligence (AI) algorithms in manufacturing evaluate intricate information, such as supply chain variables, equipment performance measurements, and production plans, to produce useful insights. Manufacturers are able to make better decisions because to this analytical capability, which increases overall productivity and eliminates operational bottlenecks.
Why Process Optimization is Important?
For firms looking to stay competitive in the fast-paced, more complicated market of today, process optimization is crucial. Businesses may increase productivity, cut expenses, and enhance overall performance by optimizing and simplifying procedures.
By ensuring that all resources whether they be labor, equipment, or materials are used efficiently, optimization reduces waste and boosts output. By facilitating quicker, more economical manufacturing, process optimization can offer a significant advantage in a setting with narrow profit margins and high consumer expectations.
Process optimization is essential for preserving product quality in addition to operational efficiency. In manufacturing, where even little flaws may result in expensive recalls or harm to a company’s brand, maintaining consistently high standards is essential. Manufacturers may reduce mistakes and ensure that goods satisfy strict standards by using strong quality control methods through optimized procedures. This promotes enduring loyalty and trust in addition to raising client happiness.
Process optimization encourages creativity and flexibility. Businesses that have streamlined their processes are better equipped to accept new tools and adapt to shifting market needs and technological advancements.
Increased flexibility from an optimized manufacturing process enables enterprises to swiftly change course, grow effectively, and investigate new prospects. In the end, process optimization is about creating a robust, future-ready business that can expand and succeed steadily, not just about enhancing present performance.
What are the Key Challenges in Traditional Manufacturing Processes?
Control of Quality and Management of Defects:
The significant issue with conventional production is maintaining constant product quality. Manual inspections are frequently used for quality control, although they can be laborious and prone to human mistakes. It gets harder to keep an eye on things when manufacturing numbers rise, which might cause flaws to slip through the gaps. In addition to causing monetary losses, defective items may damage a business’s reputation.
Manufacturers must put in place more automated and data-driven quality control procedures in order to overcome this obstacle. Real-time production monitoring, anomaly detection, and remedial action before flaws affect the finished product are all possible with these technologies.
Waste and Inefficiency:
Inefficiency, which is frequently brought on by antiquated equipment, manual workflows, and disjointed systems, is one of the biggest problems with traditional manufacturing processes. Longer manufacturing times, higher expenses, and excessive material and energy waste are the results of these inefficiencies.
Traditional setups cause overproduction or underutilization since machines follow established timetables rather than current demand. Furthermore, in manual operations, human mistakes can exacerbate inefficiencies, resulting in delays, rework, and variable product quality. A comprehensive evaluation of processes and the use of more flexible, data-driven techniques are necessary to address inefficiencies and maximize resource utilization while streamlining production.
Restricted Scalability and Flexibility:
Conventional production methods frequently find it difficult to adjust to shifting consumer tastes and market needs. Smaller manufacturing batches or customization cannot be accommodated by rigid production processes built for large output. A manufacturer’s capacity to innovate or swiftly change course in response to fresh possibilities or difficulties is hampered by this rigidity.
It can be costly and take a lot of time to increase production to meet changing demand, especially with old systems. Flexible and scalable processes are crucial for businesses to remain competitive. They help companies produce a wide range of products without losing quality or profits.
What are the Key Benefits of Artificial Intelligence (AI ) in Processes Optimization?
Improved Defect Detection and Quality Control:
The way that manufacturers identify and handle flaws is being revolutionized by AI-powered quality control systems. Manual inspections are frequently used in traditional quality checks, however they can be unreliable and prone to mistakes. AI, on the other hand, automatically and very accurately detects flaws using machine learning algorithms and picture recognition.
By analyzing thousands of goods in real-time, these systems make sure that only those that satisfy quality requirements move on to the next stage of manufacturing. AI helps firms save waste, improve customer happiness, and preserve brand reputation by lowering faults and enhancing product quality.
Enhanced Production Scheduling and Resource Allocation:
AI is particularly good at scheduling production and allocating resources, two crucial aspects of process efficiency. To generate the best production schedules, AI algorithms may examine a variety of factors, including supply chain dynamics, labor availability, and demand projections. These timetables guarantee that resources are used efficiently, cutting down on waste and idle time.
AI is also capable of dynamically modifying production schedules in reaction to unforeseen circumstances, such as equipment failures or changes in consumer demand. Even in complicated and changing contexts, producers can retain productivity and achieve delivery schedules thanks to this degree of adaptability.
Reducing Downtime and Predictive Maintenance:
By switching from reactive to predictive maintenance, AI improves maintenance strategies. Usually, maintenance happens after a breakdown or at set times. Both methods can be costly and inconvenient. AI systems analyze sensor data from machines to predict when a machine might fail. This allows for quick repairs before problems occur.
This approach extends the life of machines and cuts down on unexpected downtime. As a result, businesses can lower maintenance costs, improve asset reliability, and maintain a steady production flow. All these factors lead to more efficient operations.
Data Analysis and Insights in Real-Time:
Because it makes real-time data analysis possible, artificial intelligence (AI) is essential to process optimization. AI systems can immediately handle enormous volumes of data, but traditional techniques of data collecting and analysis are frequently static and time-consuming. With the use of this technology, manufacturers may quickly discover bottlenecks, inefficiencies, and areas for improvement and obtain actionable information.
AI-powered solutions, for example, may track machine performance and identify irregularities before they become serious problems. Businesses may optimize overall operations by using AI’s capacity to identify patterns and trends to inform data-driven choices that increase productivity and decrease downtime.
How to implement AI Solutions for Process Optimization within your Organizations
Select the Best AI Tools
First of all , you have to select the finest AI tools and technologies to suit your particular requirements. Depending on your objectives, you may need to leverage technologies like computer vision, machine learning, or predictive analytics. For instance, computer vision is particularly useful for visual inspections and defect identification, while machine learning models may be used to forecast problems or optimize operations.
Predictive analytics tools are helpful in anticipating maintenance needs. You must choose technologies that work with your existing systems and infrastructure to guarantee smooth integration and scalability for future needs.
Data Collection and Configuration of the Infrastructure"
Gathering relevant data is crucial for training your AI models, as data is the foundation of any AI application. This includes sensor data, production data from the past, and any other inputs pertaining to manufacturing. Since AI models rely on high-quality data to function properly, accurate, clear, and organised data are crucial.
Set up the needed infrastructure. Make sure it connects with your current ERP or MES systems. This will allow for data collection and storage. Installing IoT sensors on manufacturing lines may be needed for real-time monitoring. These sensors collect data on factors like vibration, temperature, and pressure. This helps with analysis and improves efficiency.
Choose the Right AI Model
Once the data has been collected and analyzed, the next step is to train AI models tailored to your quality control processes. This means putting the data into machine learning techniques or deep learning models for computer vision applications.
For example, machine learning models can learn to find defects using past data. However, computer vision systems need many labeled photos to spot product issues. Customization is important to make sure the AI models fit your production environment and product details. Testing, validation, and iteration are key to making sure the models work well in real-life situations.
Pilot Testing and Validation
Before using AI systems in your entire production line, run a pilot test. This test will help you check the system’s performance in a controlled setting. Focus the pilot on a small part of your manufacturing process. This will help you validate the AI models and see how they affect quality control.
During this phase, monitor the AI system’s ability to spot errors, optimize workflows, and predict maintenance needs. Consult with operators and quality control teams to identify any issues or possible areas for improvement. Make the necessary adjustments to the AI models or system integration before scaling the solution.
What are the Main Technologies Behind the use of AI in Process Optimizations?
Predictive Analytics: Time Series Forecasting and Anomaly Detection
AI quality control predictive analytics uses anomaly detection models and time-series forecasting to anticipate possible production process failures. To examine past production data and forecast future trends, time-series forecasting methods like LSTM (Long Short-Term Memory) networks and ARIMA (AutoRegressive Integrated Moving Average) are used.
Based on factors like temperature, humidity, or equipment wear, these models assist in identifying departures from typical patterns, allowing the system to forecast when a quality problem is likely to arise. Unusual patterns in the production data can also be found using AI algorithms for anomaly detection, such as statistical approaches like clustering (e.g., k-means) or more sophisticated strategies like autoencoders. Predictive analytics, which continuously learns from incoming data, not only detects possible quality problems but also enables manufacturers to optimize maintenance schedules.
Machine Learning Models: Supervised, Unsupervised, and Reinforcement Learning
In AI-driven quality control, machine learning models cover a variety of methods, each with a distinct set of uses. Labeled datasets are necessary for supervised learning, which is commonly used for tasks like identifying defective versus non-defective products based on characteristics like size or color. For this task, algorithms like Random Forests, decision trees, and Support Vector Machines (SVM) are frequently used.
Conversely, when labeled data is limited, unsupervised learning is employed for anomaly detection and clustering. Similar product features can be grouped together and outliers that might point to flaws can be found using algorithms like K-means or DBSCAN (Density-Based Spatial Clustering of Applications with Noise). Although it is less frequently used in quality control.
Computer Vision: Advanced Image Processing and Feature Extraction
Computer vision, which is at the core of AI-driven quality control, uses sophisticated image-processing methods to examine products. The system takes detailed pictures of the products on the production line using high-definition cameras. After that, feature extraction algorithms are used to process these photos in order to find important components like edges, textures, and shapes.
These features are analyzed hierarchically using deep learning models, specifically Convolutional Neural Networks (CNNs), which simulate how people interpret visual information. The system can identify anomalies like cracks, scratches, or alignment problems because these networks are trained on enormous datasets of labeled images. The system can also confirm labels or serial numbers by using methods like optical character recognition (OCR).
Robotic Process Automation (RPA)
The technique known as robotic process automation (RPA) uses software bots to automate repetitive, rule-based processes that are normally completed by people. RPA focuses on automating digital activities including data input, order processing, and report production, in contrast to conventional industrial robots that do physical tasks. RPA bots are faster and more accurate than human users when interacting with databases, systems, and applications.
RPA is essential for optimizing operational and administrative procedures in the manufacturing industry. RPA, for example, may automate inventory management by creating purchase orders when supplies run short and updating stock levels in real-time. Additionally, it can manage supplier communications, process invoices, and provide compliance reports. RPA decreases human error, increases productivity, and enables these repetitive operations to be automated.
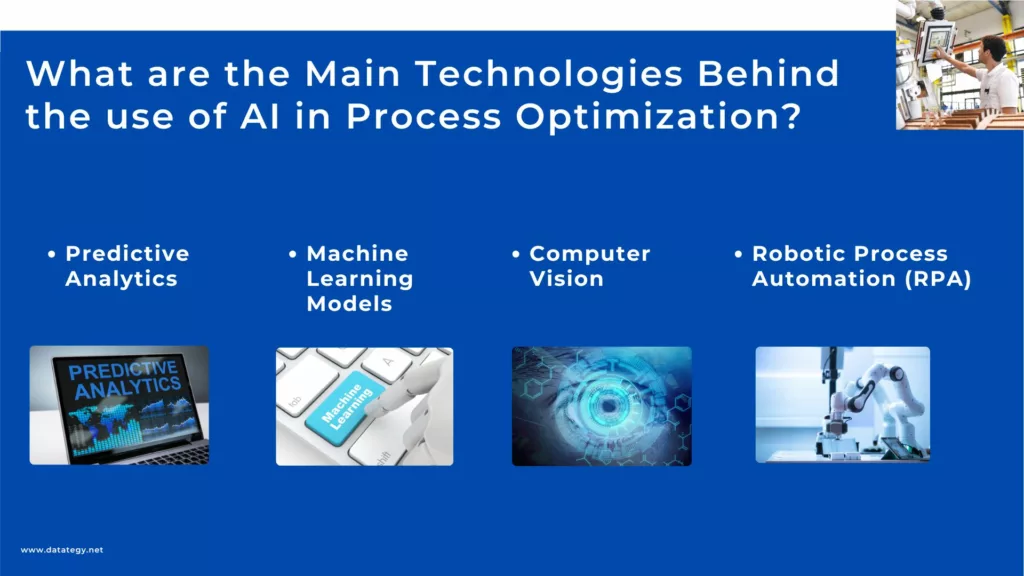
Main Technologies Behind AI in Quality Control
Real-world Examples of Process Optimization using Artificial Intelligence
Honeywell: Enhanced Production Scheduling Through AI
Honeywell’s production scheduling procedures throughout its manufacturing sites are greatly improved by utilizing artificial intelligence. Large volumes of data from sensors and other IoT devices placed around the manufacturing floor are analyzed by the company’s AI-driven solutions. This data contains up-to-date information on environmental conditions, supply chain logistics, worker availability, and machine status.
Advanced machine learning techniques are used by Honeywell’s AI systems to forecast possible production line interruptions, such as supply chain delays or equipment problems. By doing this, the AI can more effectively distribute resources, make proactive schedule adjustments, and guarantee that production deadlines are fulfilled. Due to faster and more dependable product delivery, lead times are shortened and customer satisfaction is raised. Source.
Siemens: Production Optimisation Driven by AI
Siemens has used artificial intelligence (AI) in its manufacturing procedures to promote creativity and efficiency. Real-time production data may be analysed by the company’s AI systems to spot inefficiencies and other problems before they get out of hand. Siemens is able to continually monitor and optimise a number of production process factors by utilizing machine learning.
Predictive maintenance is one important way AI is being used at Siemens. In order to save downtime and prevent unplanned equipment breakdowns, the AI systems track the functioning of the machinery and forecast when maintenance is necessary. This guarantees smooth and effective output in addition to extending the equipment’s lifespan.
Siemens uses AI for quality control. Machine learning models are trained to detect defects in products with high accuracy. By identifying defects early in the production process, Siemens can take corrective actions promptly, ensuring that only top-quality products reach customers. This improves customer satisfaction and reduces the cost of rework and scrap. Source.
Beko: Using AI to Transform Manufacturing Processes
Leading home appliance maker Beko uses AI-driven advancements to streamline its production procedures. Beko has reduced fault rates and significantly reduced material costs by incorporating AI technology. To find bottlenecks, simplify processes, and recommend enhancements, the AI systems examine production data.
Predictive maintenance is one of the primary advantages of AI at Beko. In order to prevent unplanned malfunctions and minimize downtime, the AI keeps an eye on the condition of the equipment and forecasts when maintenance is required. This prolongs the equipment’s lifespan and increases overall production efficiency.
Process optimization is another key component of Beko’s AI-driven strategy. To find areas that need development, the AI systems examine data from different manufacturing phases. To improve efficiency, the AI may, for instance, advise modifying the process or the production schedule. Beko is able to sustain its competitive advantage in the home appliance sector thanks to this ongoing optimization. Source.
AstraZeneca : AI-Powered Drug Development and Production
In order to maximize the physical and chemical characteristics of active pharmaceutical ingredients (APIs), AstraZeneca utilises AI in medication development and manufacture. AI-driven models forecast the performance of APIs in production, enabling modifications to guarantee quality and consistency.
AI is also utilized in the formulation process to create medication items that are both stable and efficient. AstraZeneca lowers expenses, expedites drug development schedules, and guarantees that novel drugs satisfy strict regulatory requirements by using AI. This strategy improves the business’s capacity to more effectively provide patients with cutting-edge treatments.
In the drug manufacturing process, AI systems analyze data from various production stages to identify potential issues and optimize workflows. For example, AI can predict the impact of different manufacturing parameters on product quality and suggest adjustments to improve consistency. This helps AstraZeneca maintain high standards of quality and compliance with regulatory requirements.Source.
Before using AI-powered Process Optimization, what obstacles must we overcome?
Expenses and Return on Investment: A significant hurdle to embracing new technology is the initial outlay required, particularly for small to medium-sized businesses. The thought of investing in sensors, data integration tools, and AI-driven systems can be intimidating. However, companies should view these costs as long-term investments that will eventually lead to cost reductions and enhanced operational efficiency.
Ensuring Dependability via Data Quality: Utilizing advanced technology such as AI-driven quality control brings additional data management and quality issues. The efficiency of machine learning and AI models can be compromised by inconsistent, absent, or incorrect data. Companies need to implement strong procedures for data gathering, storage, and examination to guarantee precision. Regular inspection of data inputs and the use of sophisticated analytics methods can enhance dependability.
How to choose the best AI solution for your data project?
In this white paper, we provide an overview of AI solutions on the market. We give you concrete guidelines to choose the solution that reinforces the collaboration between your teams.
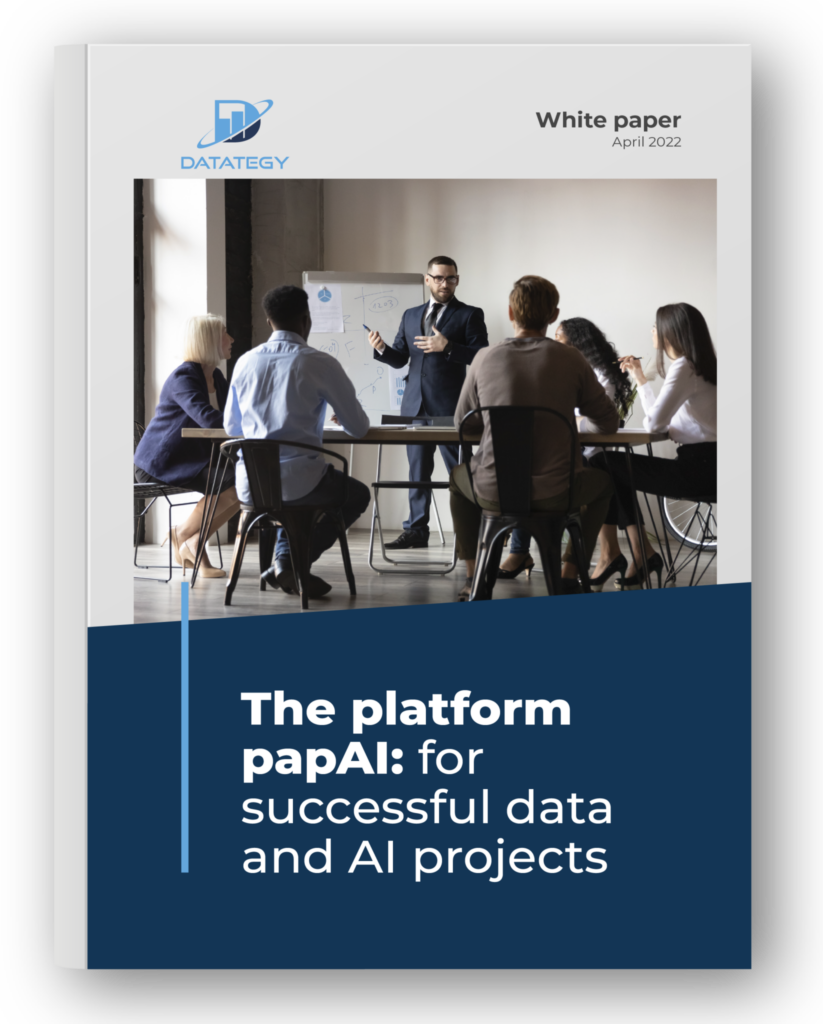
How papAI Helps Build Effective AI-Powered Process Optimization?
papAI is a comprehensive artificial intelligence solution made to optimize and simplify processes in a variety of sectors. It offers strong data analysis, predictive insights, and process automation capabilities by fusing state-of-the-art machine learning and artificial intelligence technology.
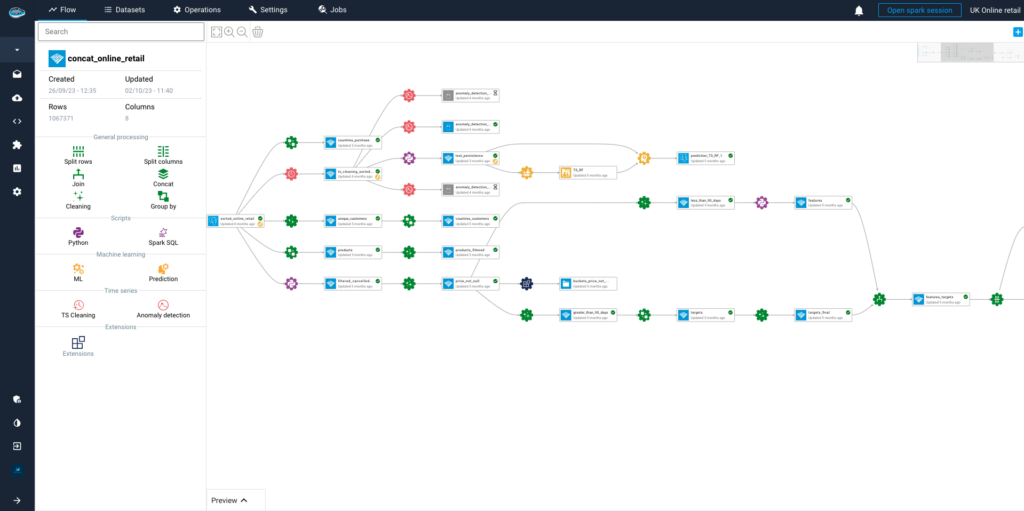
Here’s an in-depth look at the key features and advantages of this innovative solution:
Data Integration and Streamlining
papAI first automatically interacts with a variety of data sources, including production logs, sensor data, and historical quality control records. It integrates massive amounts of data from many systems (such MES and ERP) onto a single platform. This interface guarantees that papAI has real-time access to all relevant production data, which is essential for accurate analysis and decision-making.
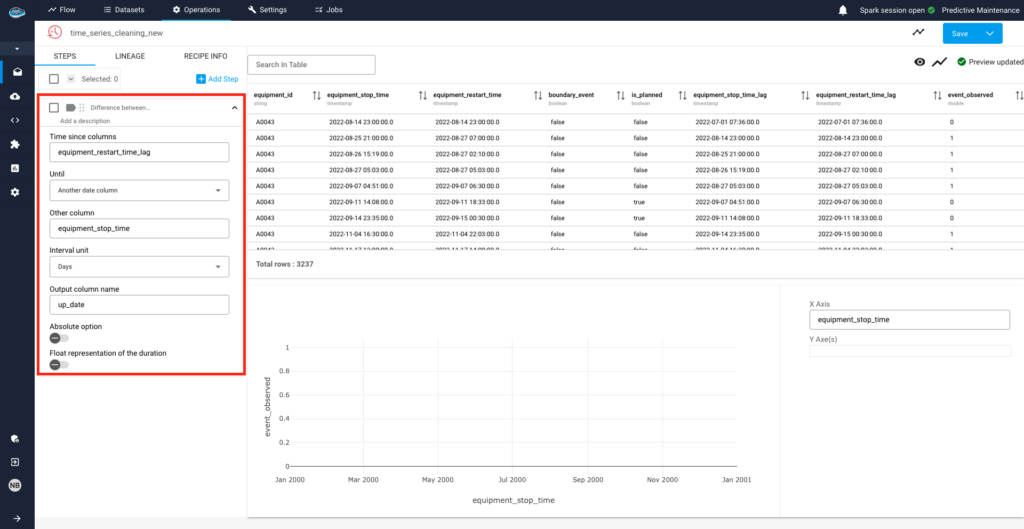
Advanced Predictive Analytics and Real-time Insights
The intelligent predictive analytics capabilities of papAI are among its primary attributes. It makes use of both historical and current data to spot trends and anticipate possible flaws or equipment failures before they happen.
papAI forecasts possible problems in the manufacturing process by analyzing production variables like temperature, pressure, and vibration using machine learning algorithms. By using these predictive insights, businesses can avoid quality problems by taking proactive measures like planning maintenance or modifying production parameters.
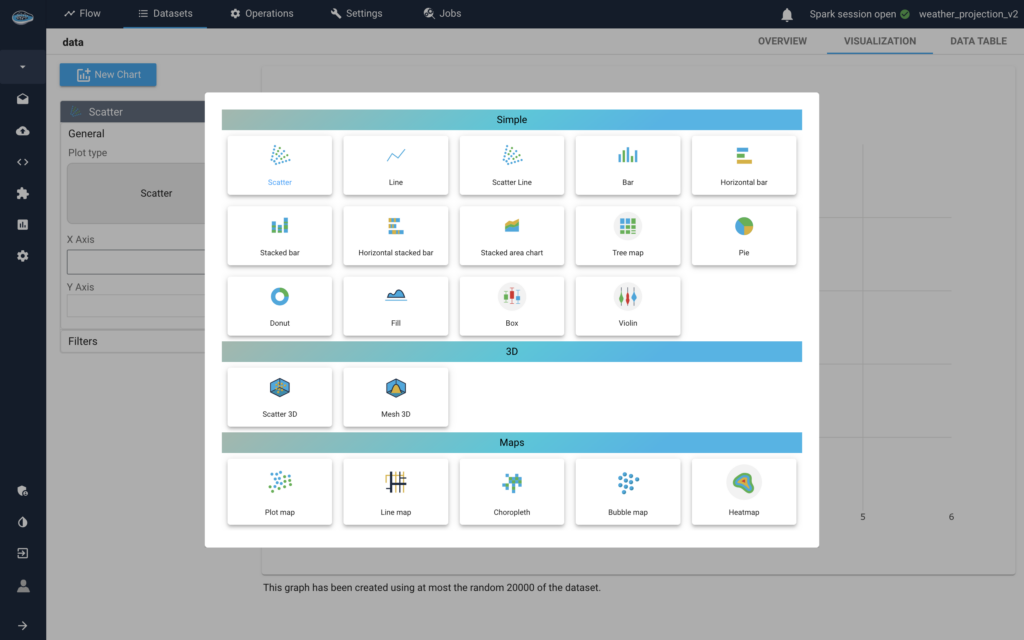
Smooth Scalability in Different Production Lines
papAI is designed to expand effortlessly across a range of production lines and manufacturing settings. Whether your company has a single manufacturing line or several lines dispersed across multiple sites, papAI can adapt to a range of production requirements and configurations. By automatically adjusting to changes in production volume, product kinds, or operating methods,
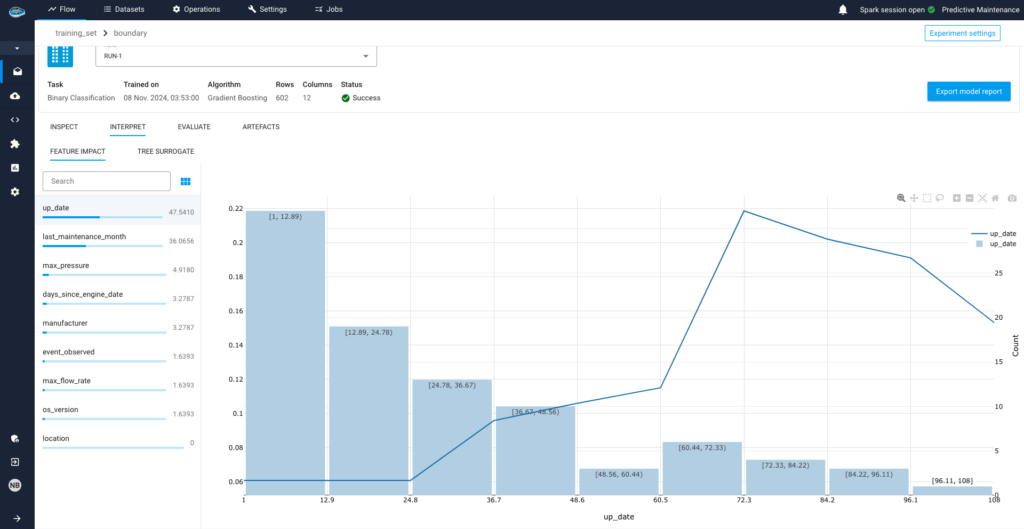
Create your Own AI-Powered Process Optimization Solution using papAI solution
Through the incorporation of cutting-edge technologies such as machine learning, computer vision, and predictive analytics, papAI is transforming process optimization, paving the way for smarter and more efficient production processes.
Because to papAI’s seamless connection with your existing systems, real-time insights, and continuous data learning, your quality control is always optimized. papAI provides you with the knowledge and resources you need to accomplish your objectives, whether they are to predict maintenance needs, reduce faults, or boost overall production efficiency.
Schedule a demo now to see how our AI solution can improve your production processes. Experience lasting increases in product quality for yourself.
AI enhances process optimization by analyzing vast datasets to streamline operations, improve decision-making, and unlock efficiencies.
Process optimization is critical because it boosts productivity, reduces costs, and enhances performance by ensuring efficient use of resources like labor, equipment, and materials. It minimizes waste and helps businesses maintain high product quality, which is essential for customer satisfaction and brand reputation..
- Quality Control: Manual inspections are time-consuming and error-prone, leading to inconsistencies.
- Waste and Inefficiency: Outdated equipment and manual workflows cause delays and resource wastage.
- Scalability and Flexibility: Rigid systems struggle to adapt to market changes and customized production needs, limiting innovation and responsiveness.
- Select the Right AI Tools: Choose technologies like machine learning, computer vision, or predictive analytics based on specific needs.
- Data Collection: Gather high-quality, relevant data and integrate it with existing systems.
- Train AI Models: Customize AI models for the production environment and validate them through pilot testing.
- Pilot and Scale: Conduct controlled pilot tests to ensure performance before full deployment, making adjustments as needed for optimal results.
Interested in discovering papAI?
Our AI expert team is at your disposal for any questions
How AgenticAI is Transforming Sales and Marketing Strategies
How AgenticAI is Transforming Sales and Marketing Strategies Agentic AI...
Read More“DATATEGY EARLY CAREERS PROGRAM” With Abdelmoumen ATMANI
“DATATEGY EARLY CAREERS PROGRAM” With Abdelmoumen ATMANI Hello, my name...
Read MoreIntroducing the Error Analysis Tree: A Smarter Way to Improve AI Models
Introducing the Error Analysis Tree: A Smarter Way to Improve...
Read More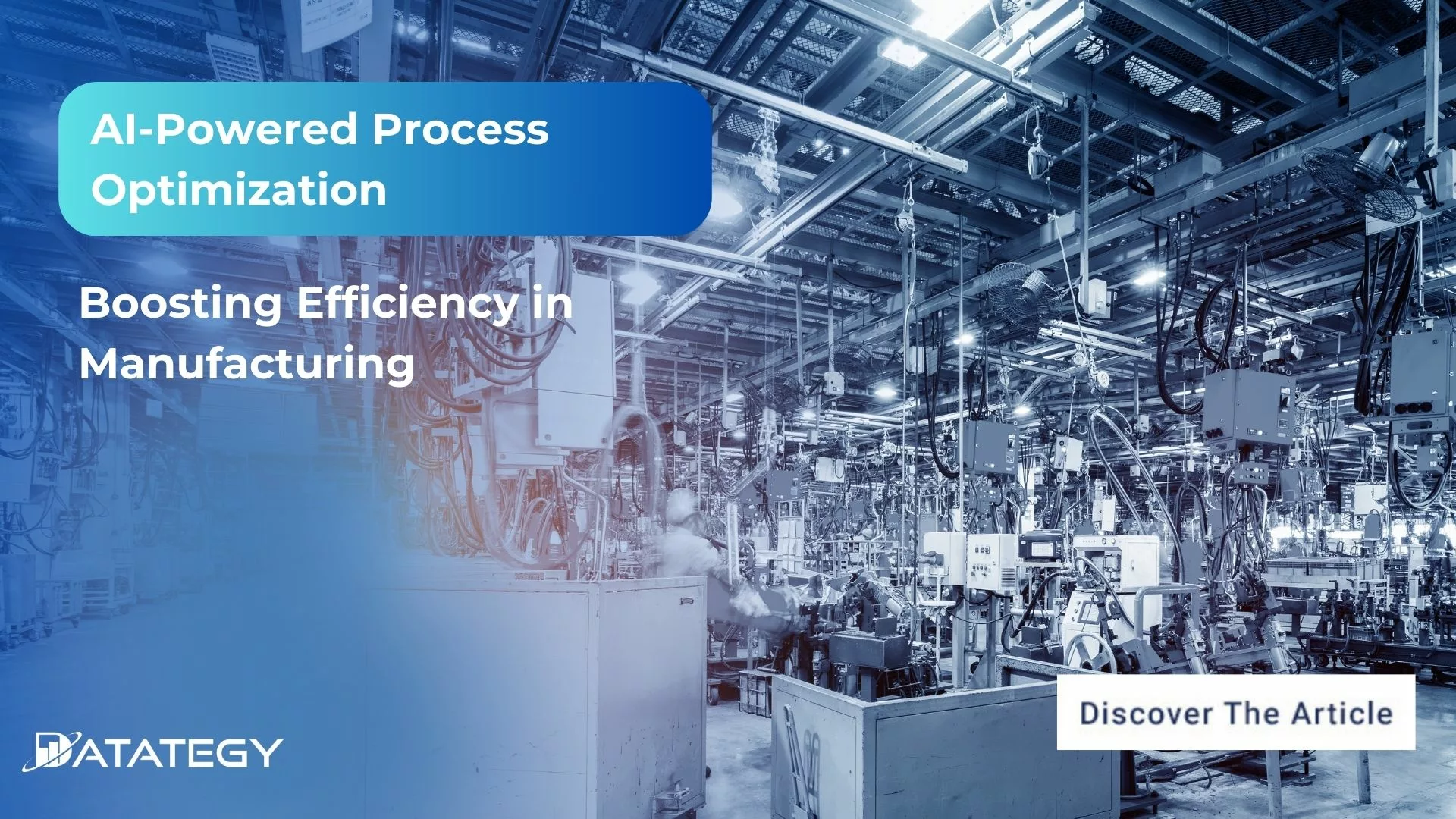
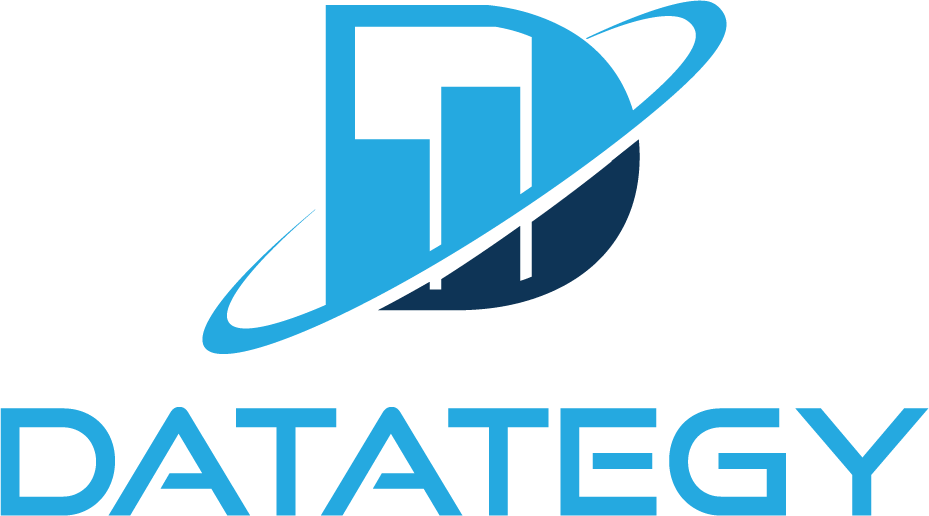