Scaling RAG Systems in Financial Organizations Artificial intelligence has emerged...
Read MoreOptimize Manufacturing with Real-Time Monitoring and Data Analysis
Table of Contents
ToggleWith every innovation wave, the manufacturing sector has changed, constantly looking for new methods to increase productivity and efficiency. Industrialization transformed production centuries ago, changing the way goods were made and causing unheard-of growth. Later, lean manufacturing redesigned operations by cutting waste and streamlining procedures.
Today, artificial intelligence, real-time monitoring, and data analysis will drive yet another transformative phase. Manufacturers now have the ability to improve product quality, make quicker, more informed decisions, and maintain flexibility in a market that is changing quickly thanks to these cutting-edge tools.
Find out how papAI can improve the deployment of AI projects in the Manufacturing Industry.
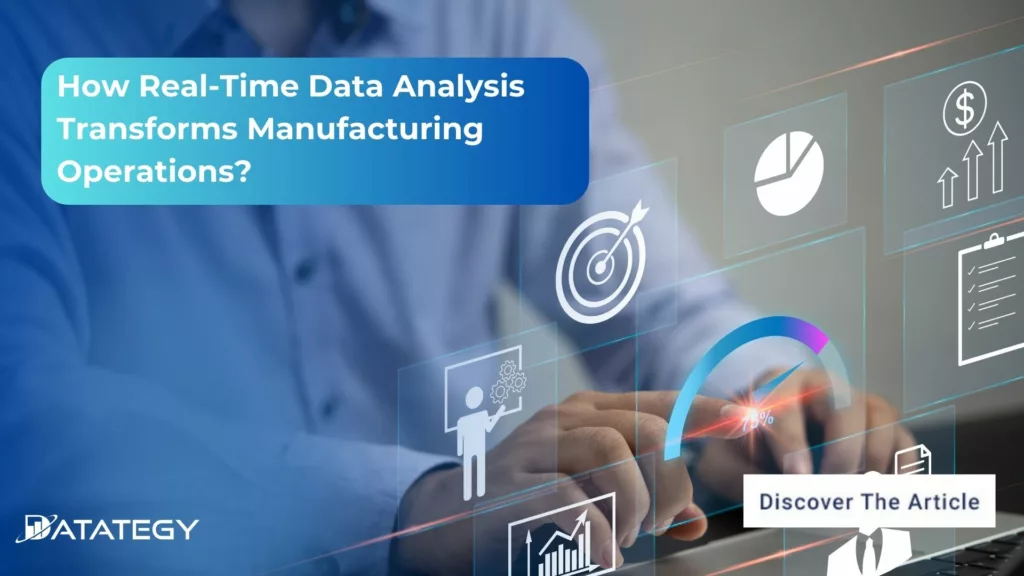
This article explores the benefits of real-time monitoring and data analysis, along with concrete use cases.
Why Real-Time Monitoring and Data Analysis are Important?
the manufacturing industry, real-time monitoring is quickly becoming indispensable. Real-time monitoring offers instant visibility into production lines, equipment health, and quality control, in contrast to traditional monitoring, which depends on recurring inspections.
Because of this constant flow of data, manufacturers are able to identify problems early on and stop minor ones from developing into expensive malfunctions or production delays. Even when demands change, managers and operators can make quick, well-informed decisions with real-time insights that maximise output, cut waste, and uphold high standards of quality.
Data analysis is crucial in the current manufacturing landscape as it allows companies to convert raw data into valuable insights that can enhance productivity and innovation. Data analysis helps manufacturers decipher the myriad of data points produced every second, from machinery efficiency to production speeds, by identifying trends, patterns, and potential areas of enhancement.
Companies can improve process efficiency, cut waste, and enhance product quality by using data analysis as a clear, evidence-based basis for decision-making instead of relying on gut feeling or conjecture. This method not only improves daily operations but also gives manufacturers a competitive edge since they can take proactive measures to resolve issues and grasp expansion prospects based on tangible insights.
What is Data analysis and real-time monitoring's core technologies?
Internet of Things (IoT)
Manufacturing real-time monitoring and data analysis depend on a combination of cutting-edge technologies, each of which contributes special capabilities that improve the intelligence and responsiveness of production lines. The Internet of Things (IoT), which links equipment, sensors, and gadgets throughout the manufacturing floor, is one of the fundamental technologies.
IoT sensors create a real-time production snapshot by continuously collecting data on everything from environmental conditions to equipment performance. This configuration enables manufacturers to track important parameters in real time, identifying inefficiencies or irregularities as soon as they occur and enabling prompt action to avoid expensive problems.
Edge Computing
Instead of sending data to a central cloud, edge computing allows it to be processed closer to where it is generated. By lowering latency, this local processing capability guarantees that real-time monitoring insights may be put to use right away.
For example, edge computing can send out an alarm or even an automated response in milliseconds if a machine exhibits symptoms of mechanical wear or overheating. In addition to facilitating quicker decision-making, this quick processing lightens the strain on cloud systems, improving the security and efficiency of data handling.
Artificial intelligence (AI) and machine learning (ML)
By providing prescriptive and predictive insights, artificial intelligence (AI) and machine learning (ML) are also revolutionising real-time monitoring and data analysis. Large volumes of data can be examined using AI algorithms to find patterns that people might miss, such early warning signs of equipment failure or subtle trends in quality control.
Manufacturers can move from reactive to proactive strategies by training machine learning models to identify these trends and forecast future events. Businesses can use AI-driven analytics for predictive maintenance, which makes sure that equipment is maintained before it breaks down, or real-time manufacturing process adjustments, which maximize output and quality.
Cloud Computing
In order to scale data processing and storage capacities, cloud computing is essential. Long-term trend analysis and more precise forecasting are made possible by manufacturers’ ability to store and retrieve vast amounts of historical data using cloud infrastructure. Global manufacturing processes may be more easily managed from a single point of view because of the cloud’s ability to provide collaboration and data exchange throughout teams and regions.
In an ever-changing business landscape, these technologies—IoT, edge computing, artificial intelligence, and cloud computing—combine to provide a strong foundation that enables manufacturers to use real-time monitoring and data analysis, resulting in increased efficiency, agility, and resilience.
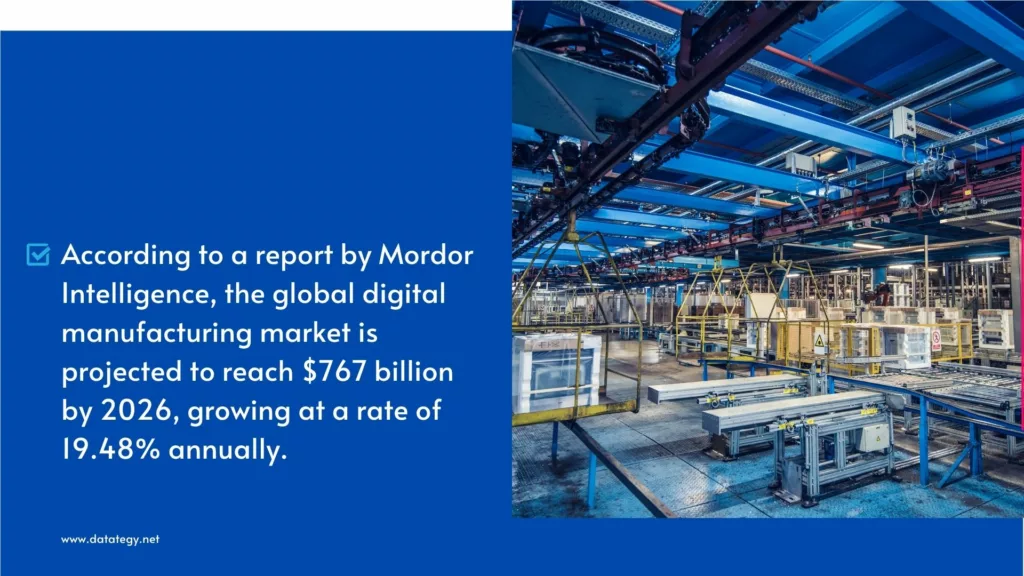
What are the Advantages of Real-Time Monitoring and Data Analysis
Enhanced Product Quality
Manufacturers may closely monitor quality parameters at every stage of production with ongoing monitoring and data analysis. Real-time data facilitates the early detection of errors or discrepancies, enabling prompt corrections. Proactive quality control helps maintain high standards that increase customer satisfaction and lessens the possibility that defective items will reach customers.
Increased Productivity and Decreased Downtime
Manufacturers are able to track every phase of manufacturing as it occurs thanks to real-time monitoring. Small problems, like as bottlenecks or equipment slowdowns, can be quickly recognized because to this visibility. Rapid reaction times allow these problems to be fixed before they cause production line disruptions, reducing expensive downtime and preserving maximum efficiency.
Cost Reduction and Predictive Maintenance
Manufacturers may anticipate when equipment may require maintenance before a problem happens by using data analysis. This predictive maintenance strategy prolongs the life of equipment, lowers repair costs, and lessens unplanned breakdowns. Manufacturers ensure a more economical operation by saving time and money by minimizing unplanned downtime.
Improved Compliance and Safety
Workplace safety is also influenced by real-time monitoring. Through constant monitoring of machinery and environmental factors, producers are able to identify risks before they endanger employees. Furthermore, data analysis lowers the danger of legal or regulatory problems by ensuring that activities meet necessary standards and maintaining compliance with safety rules.
Increasing Safety Requirements
Environmental variables including temperature, pressure, and air quality are tracked by real-time monitoring systems, which aid in spotting any risks before they have an adverse effect on worker safety. Manufacturers may satisfy compliance standards and promote employee well-being by promptly implementing remedial steps to guarantee a safe working environment with real-time warnings.
What Challenges need to be Overcome before Implementing Real-Time Monitoring and Data Analysis Platform?
Ensuring Data Quality and Accuracy
Accurate and trustworthy data must be gathered in order for real-time monitoring to be successful. Poor or inconsistent data might result in inaccurate conclusions and choices. To maintain good data quality, it is crucial to evaluate data sources, make sure sensors are calibrated correctly, and set up procedures for data validation prior to deployment.
Dealing with Overwhelming Data
Massive volumes of data are produced every second by real-time monitoring, which, if improperly handled, can overload computers. To concentrate solely on the most pertinent information, businesses must have a well-defined plan for handling, storing, and filtering this data. Overload may be prevented by putting data management systems into place and establishing guidelines for actionable data.
Providing Future Compatibility and Scalability
A real-time monitoring platform should be scalable to accommodate future expansion and technological developments in addition to meeting present demands. Manufacturers must choose a system that is both versatile and adaptive so that it can include upcoming changes and expansions. Making ensuring that various platform solutions are scalable can assist guarantee long-term success.
Connecting with Current Systems
Many producers use outdated technologies that could be difficult to integrate with modern real-time monitoring systems. It might be difficult to ensure that new data analytics tools and current technologies integrate seamlessly. A system where old and new technologies can interact efficiently may be created with the assistance of integration professionals and a comprehensive evaluation of the present infrastructure.
Datategy Magazine: AI Industrialization & Future Challenges
Datategy Magazine serves as your premier source for in-depth data insights, offering comprehensive coverage of the latest trends, strategies, and developments in the data industry. With a focus on AI industrialization and future challenges, we provide valuable analysis and expert commentary to help you stay ahead in this rapidly evolving landscape.
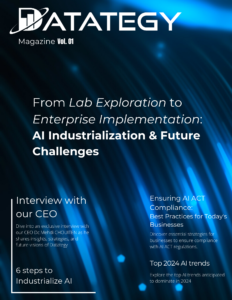
What are the Advantages to use papAI in that case?
Seamless Integration with IoT Devices
papAI is an All-in-One AI solution made to optimize and simplify processes in a variety of sectors. It offers strong capabilities for data analysis, predictive insights, and process automation by fusing state-of-the-art artificial intelligence and machine learning technology.
With papAI, companies can effortlessly track data in real-time, automate repetitive processes, and obtain useful insights that boost productivity, cut expenses, and improve decision-making. PapAI provides a scalable and adaptable platform that enables businesses to fully utilize AI, promoting innovation and growth in a variety of industries, including manufacturing.
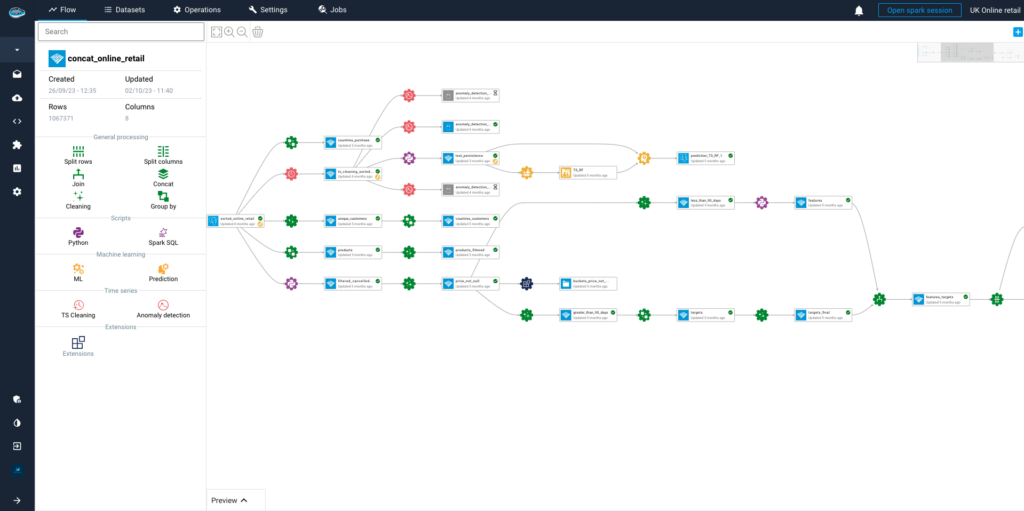
Here’s an in-depth look at the key features and advantages of this innovative solution:
Seamless Integration with IoT Devices
Data collection from equipment, sensors, and other smart devices on the factory floor is made easy by papAI’s ability to connect to a variety of IoT devices. Manufacturers may receive real-time data without complex setups or disruptions thanks to this seamless interface, which enables more accurate insights and more efficient operations.
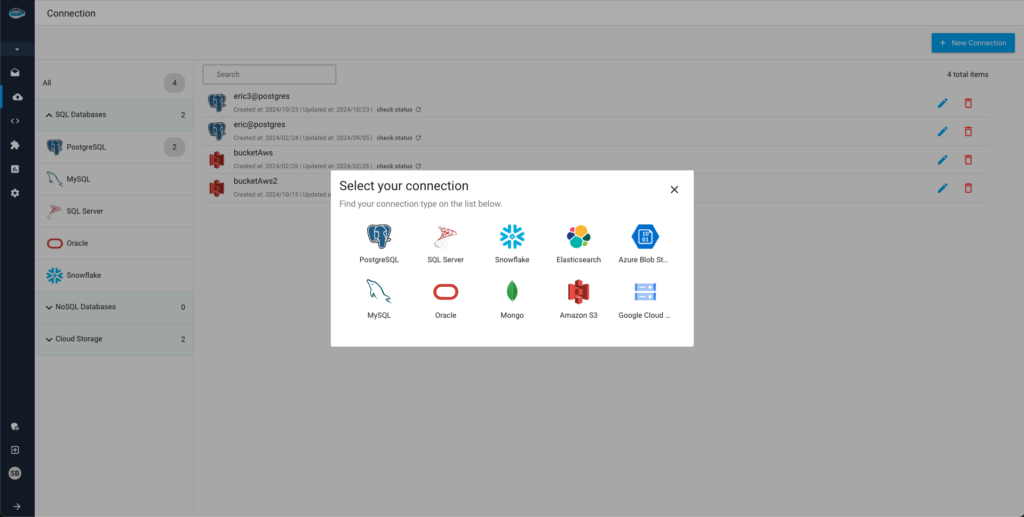
Robust API Support for Third-Party Tools
Because of its strong API support, papAI can integrate with a wide range of third-party solutions that manufacturers may already be using. Because of its adaptability, papAI can be more easily integrated into current workflows, allowing users to retain their favourite tools while still taking advantage of papAI’s sophisticated analytical features. Without requiring a whole redesign of existing systems, it improves productivity and simplifies operations.
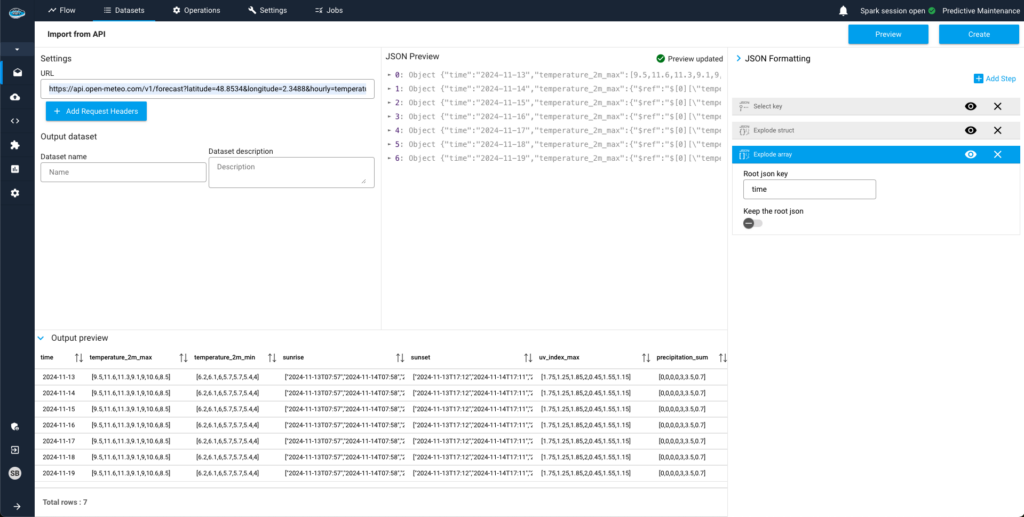
Comprehensive Data Analytics and Visualization Tools
Users may access robust data analytics and visualisation capabilities using papAI, which makes deciphering complicated data easier. Through transparent, graphical dashboards, papAI transforms unstructured data into insightful knowledge, ranging from trend analysis to predictive analytics. These solutions increase productivity and production quality by enabling firms to optimise processes, monitor KPIs with ease, and make data-driven choices more quickly.
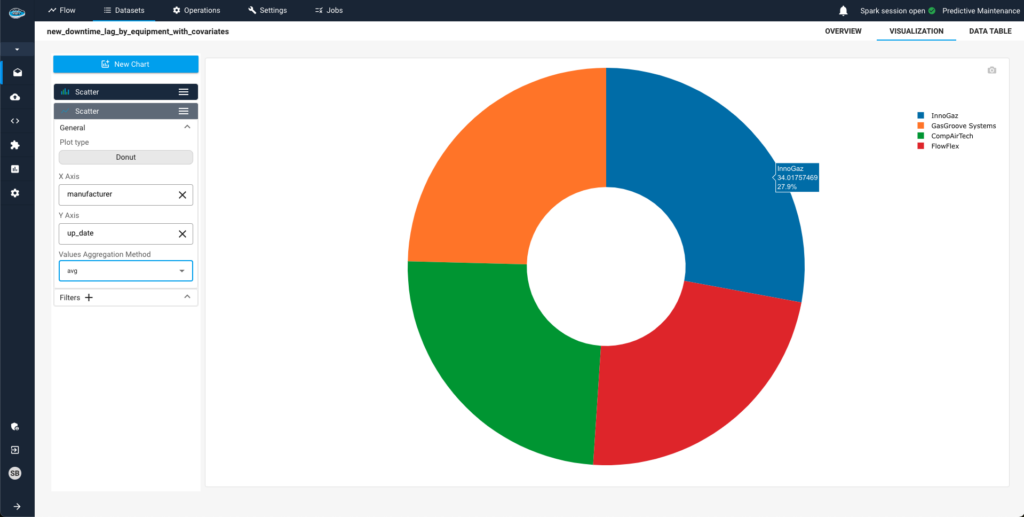
Use Real-Time Monitoring and Data Analysis with papAI solution
For manufacturing units aiming to boost efficiency, reduce idle time, and sustain their competitive edge in a swiftly evolving market, the incorporation of real-time tracking and data interpretation with the papAI solution is groundbreaking. Leveraging papAI’s seamless integration capabilities, powerful analytics, and intuitive visualizations, you can enhance product quality and make more enlightened decisions.
Are you prepared to see how your operations may be transformed using papAI? To experience firsthand the impact that intelligent, real-time monitoring can have on your company, schedule a demo with our AI and data specialists right now.
Real-time monitoring offers manufacturers immediate visibility into production processes, enabling them to detect issues early and make quick, data-driven decisions. This proactive approach minimizes downtime, reduces costs, and ensures high-quality products, giving businesses a competitive edge.
Data analysis is essential for turning the vast amounts of data generated in real-time monitoring into valuable insights. By identifying trends and patterns, manufacturers can improve productivity, optimize processes, and make informed decisions, moving from reactive to proactive management.
Real-time monitoring and data analysis are made possible by important technologies including cloud computing, edge computing, artificial intelligence, and the Internet of Things. Together, these technologies give manufacturers useful information, facilitate better decision-making, and increase scalability, all of which lead to increased operational resilience and efficiency.
Interested in discovering papAI?
Our AI expert team is at your disposal for any questions
How AgenticAI is Transforming Sales and Marketing Strategies
How AgenticAI is Transforming Sales and Marketing Strategies Agentic AI...
Read More“DATATEGY EARLY CAREERS PROGRAM” With Abdelmoumen ATMANI
“DATATEGY EARLY CAREERS PROGRAM” With Abdelmoumen ATMANI Hello, my name...
Read MoreIntroducing the Error Analysis Tree: A Smarter Way to Improve AI Models
Introducing the Error Analysis Tree: A Smarter Way to Improve...
Read More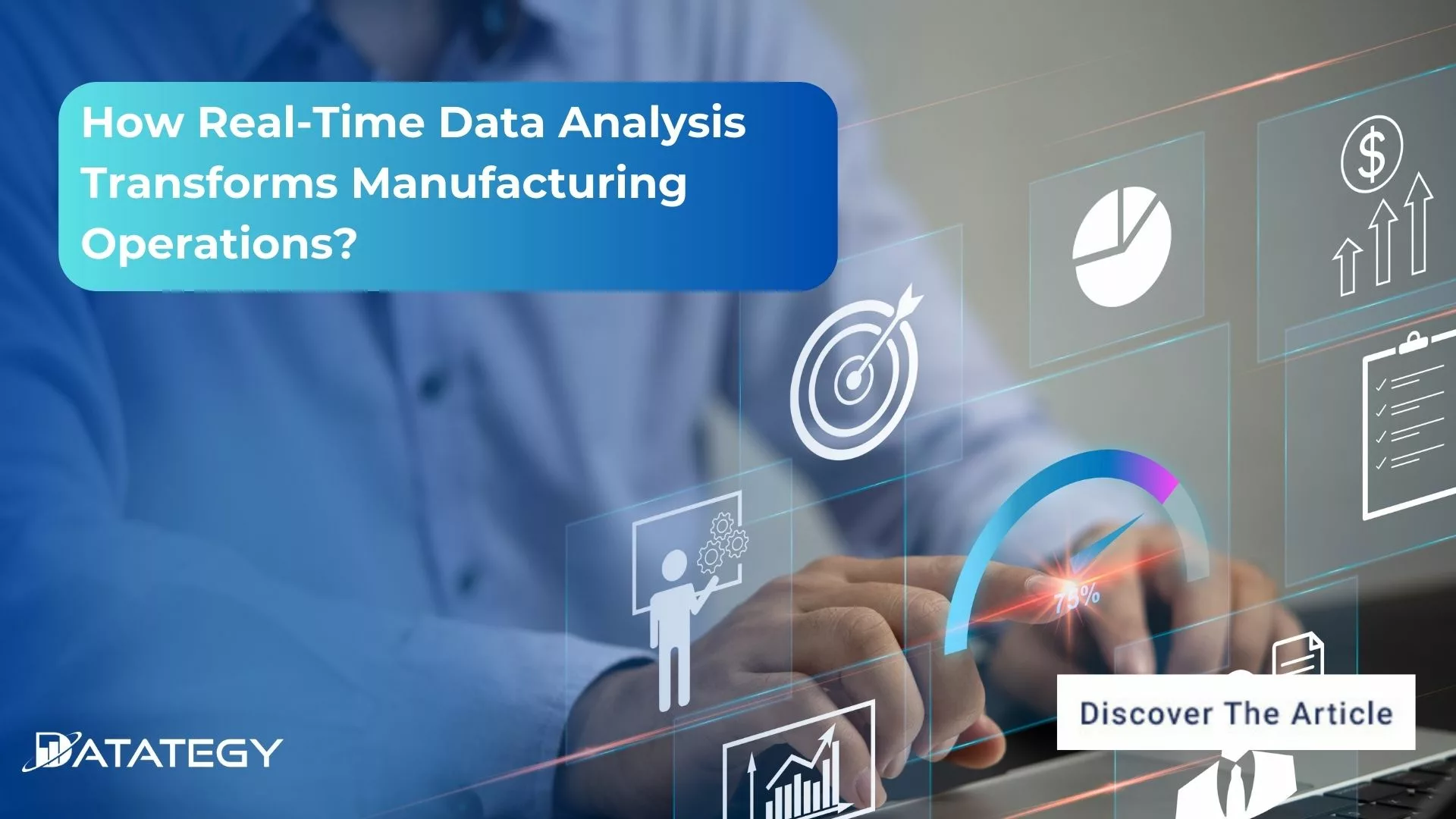
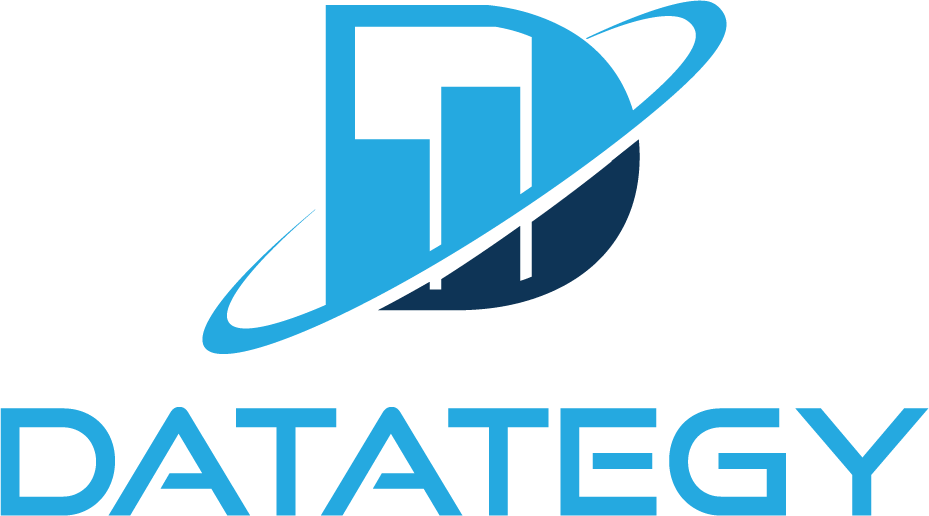