How Law Firms Use RAG to Boost Legal Research RAG...
Read MoreFueling Success:
AI Predictive Maintenance in Oil & Gas Industry
Table of Contents
ToggleThe oil and gas industry is one of the economy’s vital sectors known for its adaptability to new technologies. One of its major problems is the predictive maintenance of equipment. A study by Accenture found that AI-powered predictive maintenance can reduce unplanned downtime by up to 50%.
Find out how papAI can improve the deployment of AI projects in the Oil and Gas Industry.
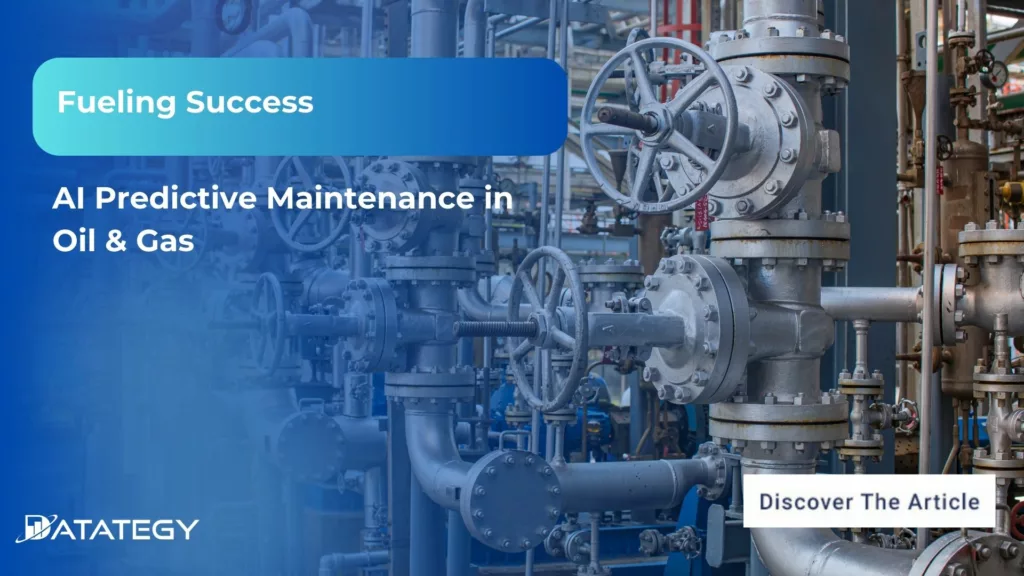
In this article, we look at concrete applications of AI to predict machine and equipment breakdowns in the oil and gas industry.
What Does Predictive Maintenance Mean?
By utilizing modern analytics and data-driven insights, predictive maintenance is a strategic technique targeted to improve the reliability as well as efficiency of industrial operations. Predictive maintenance, at its heart, is the proactive forecasting of equipment breakdowns ahead of time, enabling organizations to accurately plan maintenance tasks as needed. This shift from reactive maintenance to proactive maintenance maximizes asset longevity, minimizes downtime, and lowers operating costs.
Overview of AI Market in Oil & Gas Industry
The global AI market value for the oil and gas industry is predicted to reach $2.9 billion by 2030.
With a nearly 30.2% market share, the predictive maintenance category led the market in 2022. The upstream oil and gas industry recorded a value share of over 51.8%, while the services segment had a larger than 41.4% part of the market.
North America held a notable market value share of more than 38% of the global AI in oil & gas market However, the Asia Pacific market for AI in oil & gas industry is expected to register the highest CAGR of 17.4%.
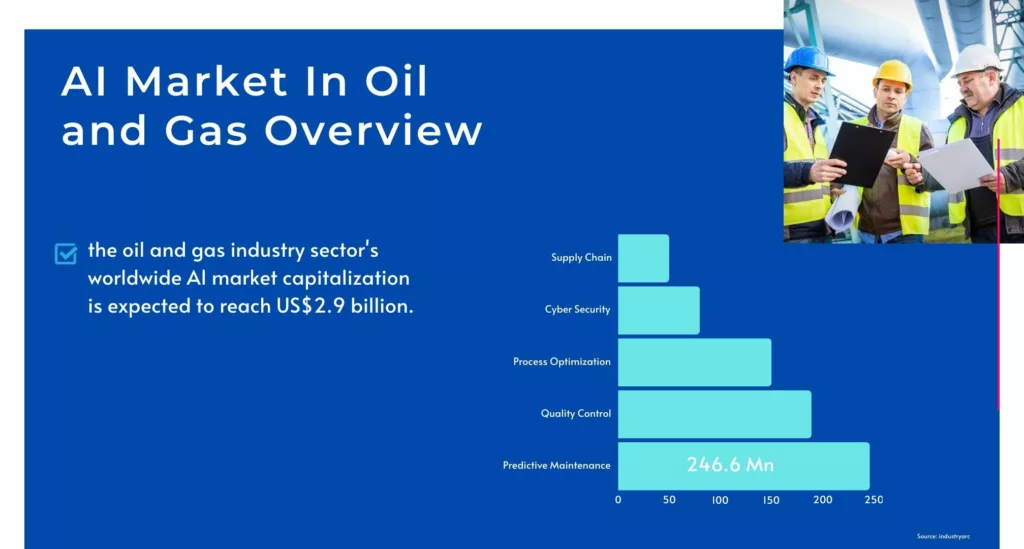
Machine Learning Algorithms (ML) as an AI-based Predictive Maintenance Engine
The oil and gas industry is witnessing a transformation in predictive maintenance largely due to machine learning (ML) algorithms. These advanced algorithms enable systems to analyze historical data, recognize patterns, and foresee potential equipment issues before they occur.
Regression and classification algorithms—two types of supervised learning models—perform exceptionally well at forecasting certain results from labeled datasets. Unsupervised learning algorithms reveal patterns and abnormalities buried inside large datasets. Examples of these models are clustering and anomaly detection. Reinforcement learning is becoming more popular for long-term maintenance strategy optimization because of its capacity for trial-and-error decision-making.
Predictive Maintenance's Practical Uses in the Oil and Gas Industry
The adoption of predictive maintenance has ushered in transformative changes, offering tangible benefits across various operational facets.
1- Pump and Compressor Health Monitoring:
Predictive maintenance is revolutionizing the way that pumps and compressors operate in the oil and gas sector, where maintaining maximum performance is vital. These crucial elements are continually and instantly monitored thanks to advanced sensor technology.
Through data stream analysis, the technology detects minute abnormalities like temperature fluctuations or variations in vibration patterns. Predictive maintenance makes targeted and timely interventions possible by anticipating possible problems before they develop into major failures. By proactively addressing wear and tear, maintenance personnel may reduce unscheduled downtime and increase the longevity of pumps and compressors. This not only increases the overall dependability of the oil and gas infrastructure and improves operating efficiency, but also saves a substantial amount of money.
2- Refinery Machinery Health Monitoring:
Predictive maintenance approaches this field by equipping refinery machinery with advanced health monitoring systems. This means that operating data from heat exchangers, motors, pumps, and other crucial parts must be continuously analyzed.
Through careful examination of parameters like temperature, pressure, and performance metrics, the system can forecast any problems with wear, corrosion, or declining efficiency. This vision enables refinery managers to precisely plan maintenance tasks, averting unplanned malfunctions that can impede output and jeopardize safety regulations.
This supports the industry’s dedication to ethical and ecological practices by fostering a safer work environment in addition to significantly reducing costs.
3- Gas Compression Station Reliability:
Essential nodes in the oil and gas network, gas compression stations are in charge of guaranteeing natural gas is transported effectively. For gas transmission networks to remain intact, the dependability of the turbines and compressors at these stations is crucial.
By putting sophisticated monitoring systems in place, predictive maintenance takes the lead in improving this reliability. Critical characteristics including vibration, temperature, and pressure are continually monitored by sensors positioned strategically throughout the station. By using real-time analysis, the system may identify variations from typical operating circumstances and alert users to possible problems before they become serious malfunctions.
4- Pipeline Leak Detection and Prevention:
Maintaining the integrity of the infrastructure is crucial in the extensive network of gas and oil pipelines, and predictive maintenance stands out as a key component in tackling the crucial problem of leak detection and prevention.
Predictive maintenance systems utilize cutting-edge sensor technology to continually scan pipelines for irregularities. These sensors gather data in real-time on temperature, pressure, and flow rates. Through the examination of these data streams, the system may spot anomalies that can point to possible leaks or structural flaws in the pipeline, enabling operators to act quickly to avert problems.
5- Hydraulic Fracturing Equipment Predictive Maintenance
In the field of hydraulic fracturing, where accuracy and dependability are critical, predictive maintenance plays a major role in guaranteeing equipment operation. Extreme conditions are applied to the sophisticated equipment used in hydraulic fracturing, including as pumps, valves, and high-pressure systems.
A network of sensors is used in predictive maintenance to continually monitor these parts. Through the examination of current data on factors like temperature, pressure, and flow rates, the system may anticipate any problems before they jeopardize the effectiveness of the hydraulic fracturing procedure.
Predictive maintenance in hydraulic fracturing is in line with safety and environmental concerns. Spills and accidents related to hydraulic fracturing operations are greatly decreased by anticipating and averting equipment breakdowns.
Real-World Application from Datategy
How is papAI platform used to detect asbestos?
SNCF Voyageurs is a company that provides passenger train services in France and across Europe. Out of its 70,000 employees, 20,000 are responsible for the industrial performance and upkeep of the rolling stock. The company oversees operations such as Voyages SNCF, TER, Transilien, Industrial Management, e-voyageurs, and the General Secretariat.
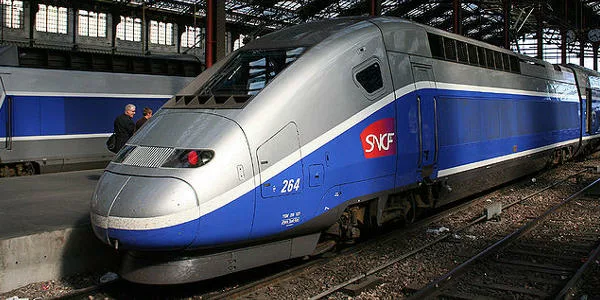
Create your Own AI-based Tool to Address Your Specific Use Case in Oil and Gas Industry using papAI
Artificial Intelligence (AI) is becoming more important in predicting and optimising maintenance tasks as the oil and gas industry’s requirement for predictive maintenance develops. Businesses are now able to use AI to make sustainable and well-informed judgements on maintenance procedures.
To find out how AI and ML could reduce the environmental effect at your business, set up a demo for a predictive maintenance AI platform. Our platform uses state-of-the-art machine learning algorithms to improve maintenance procedures, optimise equipment dependability, minimise downtime, and extend asset lifespan.
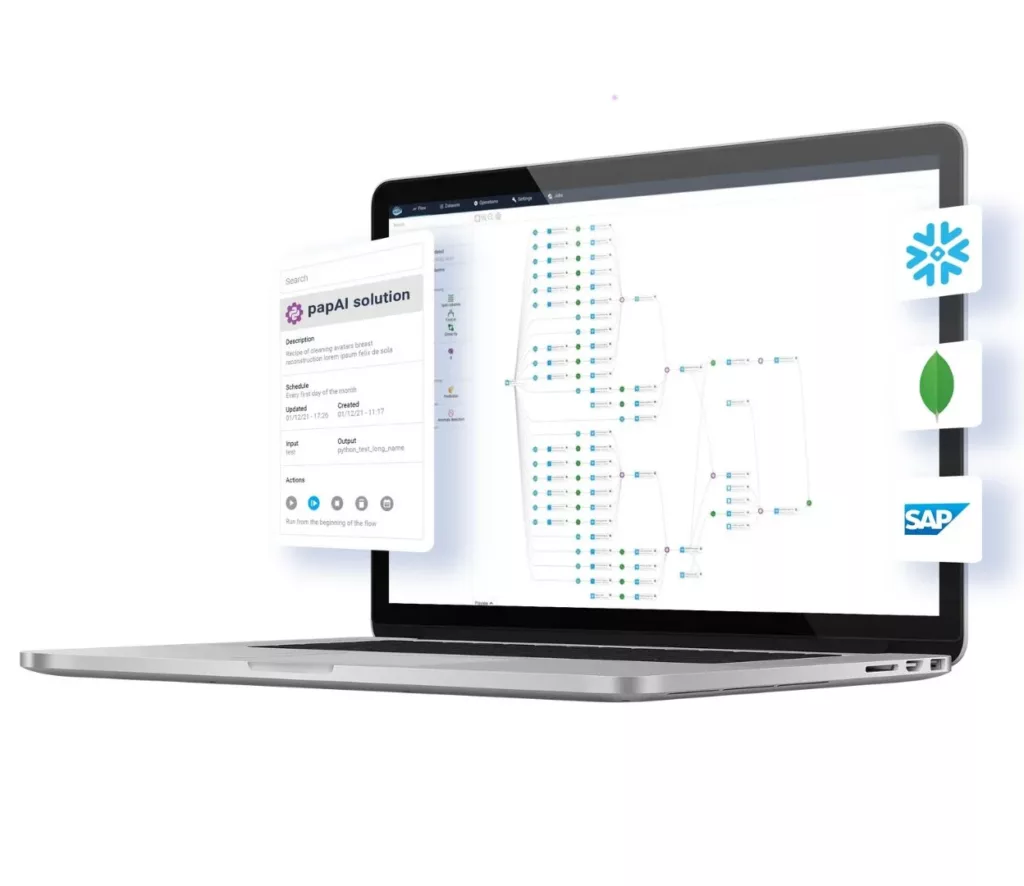
Interested in discovering papAI
Our team of AI experts will be happy to answer any questions you may have
How RAG Systems Improve Public Sector Management
How RAG Systems Improve Public Sector Management The most important...
Read MoreScaling RAG Systems in Financial Organizations
Scaling RAG Systems in Financial Organizations Artificial intelligence has emerged...
Read MoreHow AgenticAI is Transforming Sales and Marketing Strategies
How AgenticAI is Transforming Sales and Marketing Strategies Agentic AI...
Read More